Favorites
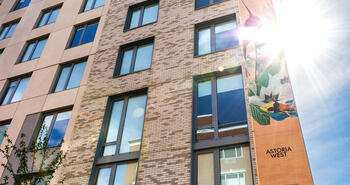
Urban Grey Klaycoat
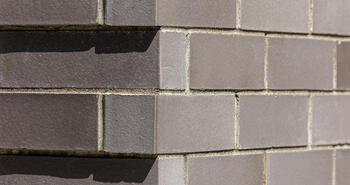
Urban Grey Klaycoat
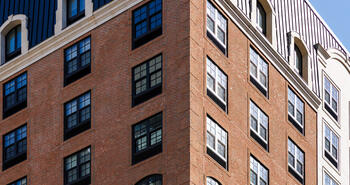
Rosewood, Thin Tech Elite
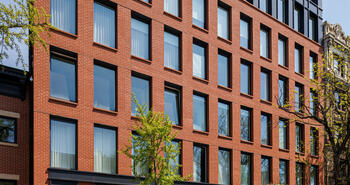
Duquesne
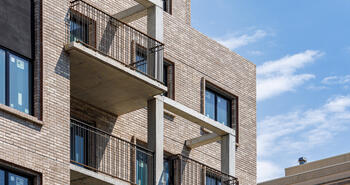
Aztec White
SKE+CHED with Design Collective
SKE+CHED ft. Design Collective
Be inspired and dive deeper into the thought process behind Alyse Talbott's work on Solaire 8200 Dixon, in the Ripley 2 district of Baltimore, Maryland.
Solaire 8200 Dixon
Custom Klaycoat Blends
View MoreYou May Also Be Interested In
We Can Help With Your Next Project
Discover the latest + greatest in design trends, industry news & pro tips from pros.
For all of your project needs, you’ll find everything you need at a Supply Center.
Let Us Know How We Can Help!
SKE+CHED with Richard Wengle Architects
SKE+CHED ft. Richard Wengle Architects
Be inspired and dive deeper into the thought process behind Richard Wengle's custom molded brick residences in the Toronto area.
You May Also Be Interested In
We Can Help With Your Next Project
Discover the latest + greatest in design trends, industry news & pro tips from pros.
For all of your project needs, you’ll find everything you need at a Supply Center.
Let Us Know How We Can Help!
SKE+CHED with Stantec
SKE+CHED ft. Stantec
Be inspired and dive deeper into the thought process behind Jennifer Grafton's work on the Northeast Community Propel Academy, in the School District of Philadelphia.
Northeast Community Propel Academy
Custom Klaycoat Blend
View MoreYou May Also Be Interested In
We Can Help With Your Next Project
Discover the latest + greatest in design trends, industry news & pro tips from pros.
For all of your project needs, you’ll find everything you need at a Supply Center.
Let Us Know How We Can Help!
Glazed Brick
To create the unmistakable look of Glazed brick, a glaze is applied to the outer surface of extruded clay and carefully fired, allowing an unlimited long-lasting color range and variation of textures from glass smooth to speckled and rough.
You May Also Be Interested In
We Can Help With Your Next Project
Discover the latest + greatest in design trends, industry news & pro tips from pros.
For all of your project needs, you’ll find everything you need at a Supply Center.
Let Us Know How We Can Help!