Design Vault Ep. 25 102 Bainbridge with Michelle Todd
ABOUT THE ARCHITECT:
![]()
|
A design firm specializing in progressive and innovative designs that enhance the environment and existing urban fabric. * Our focus is to design and develop projects that are sensitive and responsible to social wellness, cradle to cradle architecture and the planet. * Better buildings. Better change.
Michelle Todd is an architect and urban community activist who has a longstanding passion for socially responsive, innovatively progressive, and restorative preservation design. Michelle grew up in Brooklyn’s Bedford-Stuyvesant neighborhood in the 1970s before it was hip, in one of Mayor John Lindsay’s modular housing developments. She knew she wanted to be an architect at ten and had big plans for the empty lot across from her apartment building.
It was the beginning of her interest in Urban Planning and how socially responsive architecture can do something positive for people and the planet. After a brief stint at Perkins Eastman, she opened her own firm in 2008. Since then, she has worked for small and large corporations such as Snapple, the New York City agency Office of Emergency Management and private residential projects. Since 2008 she has since set up her own studio in Brooklyn, New York and focuses on historic renovations and additions to collaborate more directly with clients and be closer to the construction process. She has worked on landmark designated buildings, bakeries, restaurants, school projects and completed dexterous renovations which push the envelope of the expected, creating simple beautiful spaces. Michelle has a Master of Science from Columbia University GSAPP in Architecture and Urban Design, where she was awarded the Lucille Smyser Lowenfish Honors Award for work in Urban Design. Master Planning of Community Developments is an initiative she is well versed in accomplishing. She is certified as a consultant with the International Institute of Building Enclosures (IIBEC) and Living Future Accredited (LFA) with the International Living Future Institute. She also studied at the famous École de Beaux-Arts in Fontainebleau, France. She is an adjunct Professor at New York City CUNY College and a licensed architect in New York State and Maryland State. You can find her gardening and planning programming with the AIA Brooklyn COTE Committee and AIA National Regional & Urban Design Committee.
|
---|
ABOUT THE PROJECT:
Residents of New York City take immense pride in their city, renowned for its vibrant energy, rich culture, and remarkable history. Among the numerous neighborhoods, Brooklyn's Bedford-Stuyvesant, fondly known as Bed-Stuy, stands out with its collection of over 8,000 buildings pre-dating the 20th century.
One of those buildings immersed in this historical tapestry is the beautiful home of 102 Bainbridge Street located in the Bedford Stuyvesant original Stuyvesant Heights Historic District which was designated on September 14th, 1971. It was built within a row of building Nos. 76-104 and is a long group of houses planned to form seven freestanding architectural units, consisting of fourteen paired houses plus a single house at the eastern end. These unusual two-story houses, designed by W. F. McCarthy, are of red brick laid in Flemish bond, and were built in 1919 for Samuel Willen, treasurer of the Prosser Construction Company. 102 Bainbridge itself is a modified Spanish Renaissance style with a triple arch loggia surmounted by a group of five (5) double hung windows. The roof parapet rises at the center in an arch supported on concave shoulders. The house is set back behind brick terraces with brick balustrades and are approached by L-shape stoops set back at a common wall.
The initiation for the restoration for this building was due to the exterior façade along the roof parapet on the west and north elevation were buckling with severe step cracking occurring along masonry segments in the façade with patches of damaged stucco. Within the west façade along the base of the stepped parapet were damaged steel tie rods. At the north façade, the center stone pediment needed to be supported correctly and coping stones above it had to be repaired. At grade, the front façade along the brick terraces walls showed signs of masonry buckling and deterioration. The entire existing roof, skylights, roof hatch and areas of limestone and blue stone above and below the windows were in dire need of repair.
The premise to rectify the structural conditions of the home began early in the design to utilize sustainable means and methods to restore the building. A major step taken was not to replace the areas along the façade again with new stucco. Stucco accounts for 8.2% of carbon emissions and is a material that is hard to maintain due to temperature change effects, dealing with moisture and freezing. During the removal process of the existing stucco along the rear east elevation the homeowners genuinely liked the appearance of the natural brick underneath. The advantage of keeping the natural brick exposed was its resilience to harsh climatic resistance, durable, low-maintenance, fireproof, noise cancelling, energy efficient and just made the building more attractive. The existing brick under the stucco in the rear of the home was a different brick color and style from the original masonry brick along the front east elevation and north elevation. We therefore chose a brick like the underlining brick called Glen Gehry Cushwa Calvert Series Middle Plantation Brick 52-DD along with 403 mortars to match masonry bond style.
As the construction project continued upon removal of the stucco face, it was revealed that a 1956 addition to 102 Bainbridge Street along the second-floor rear east and south façade was framed with wood along the exterior instead of masonry as per the original blueprints and approval submitted. Even though this construction was done before the landmark designation in 1971, the use of wood was illegal back then and present-day NYC building code because the building is along a shared property line with an adjacent building. This plot twist made the project move from being an exterior renovation to a demolition and reconstruction of a new addition.
To address this issue, the structural engineering firm Silman Structural Engineering was brought in to provide consultation on the next steps. Their recommendation was to reuse the existing steel lintels that were located under the wood along the exterior façade where the original windows were located and the roof structure. An entirely new structural design was created to merge the old methodologies of the 2-wythe masonry wall with the new steel framing from Marino\WARE. Scott Hughes Principal Director of Structural Engineering at Silman stated he specified Marino-Ware products because of the wealth of publicly available published information about them and their sustainable qualities of steel being robust, long-lasting, and 100% recyclable, making it unmatched by most other building materials in terms of its lifecycle. The new wall construction entailed the structural steel from Marino Ware which has the environmental product declaration from UL, USG glass mat sheathing made of recycled material and is 100% recyclable, the Blueskin vapor barrier to contribute the energy efficiency of the home and Glen Gehry bricks for the 2-wythe exterior wall. The existing steel lintels rediscovered remained to install the original style windows back at those locations along the east and south façade.
In correcting the existing parapet at the roof, we replaced the existing steel tie rods with the assistance of a local steel maker in Brooklyn who created each unique piece separately. This became handy when we had to go back to him again to create additional steel tie rods, upon the demolition of the top parapet along the north façade. There it was discovered the masonry construction was three wythe and within it were steel tie rods hidden from view to support the center of the arch with the stone pediment along with the concave shoulders.
The masonry wall along the front porch during the demolition process existing bricks were analyzed closely to see which ones could be salvaged and reused. This helped to maintain the budget of the project but also to have less impact to add to the wasteful construction materials to landfills which brick encompasses about 6.54% sadly. Areas within the masonry façade that were in decent shape stayed and dilapidated areas were replaced with new bricks. The entire roof was professionally abated and replaced using Siplast roofing system which uses reusable insulation to bright white liquid-applied roof membranes and granule surface that helps reduce atmospheric pollution. The environmental and sustainable goals were met with the reduction of building energy use, increase roof longevity and reduction of urban heat island effect. The large skylight was replicated and replaced. The small skylight on the roof was replaced with an operable solar skylight which aids natural light and ventilation to come into the building.
All existing coping stones were cleaned, repaired, reused, and restored. New limestone and blue stone used in the restoration was advocated from quarries and manufacturers who met ANSI/NSC 373 Standard.
Completing the exterior façade restoration entailed the replacement of the steel window lintels for some of the existing windows. The steel used was recyclable. The homeowners desired to have all the windows replaced for the home to save energy, save money obtain ultimate insulation, climate control, more light, less noise, dust, and outside pollutants. The windows was provided by Norwood Window and Doors because of their strong advocacy of their products created from sustainable harvested lumber and NRFC rating.
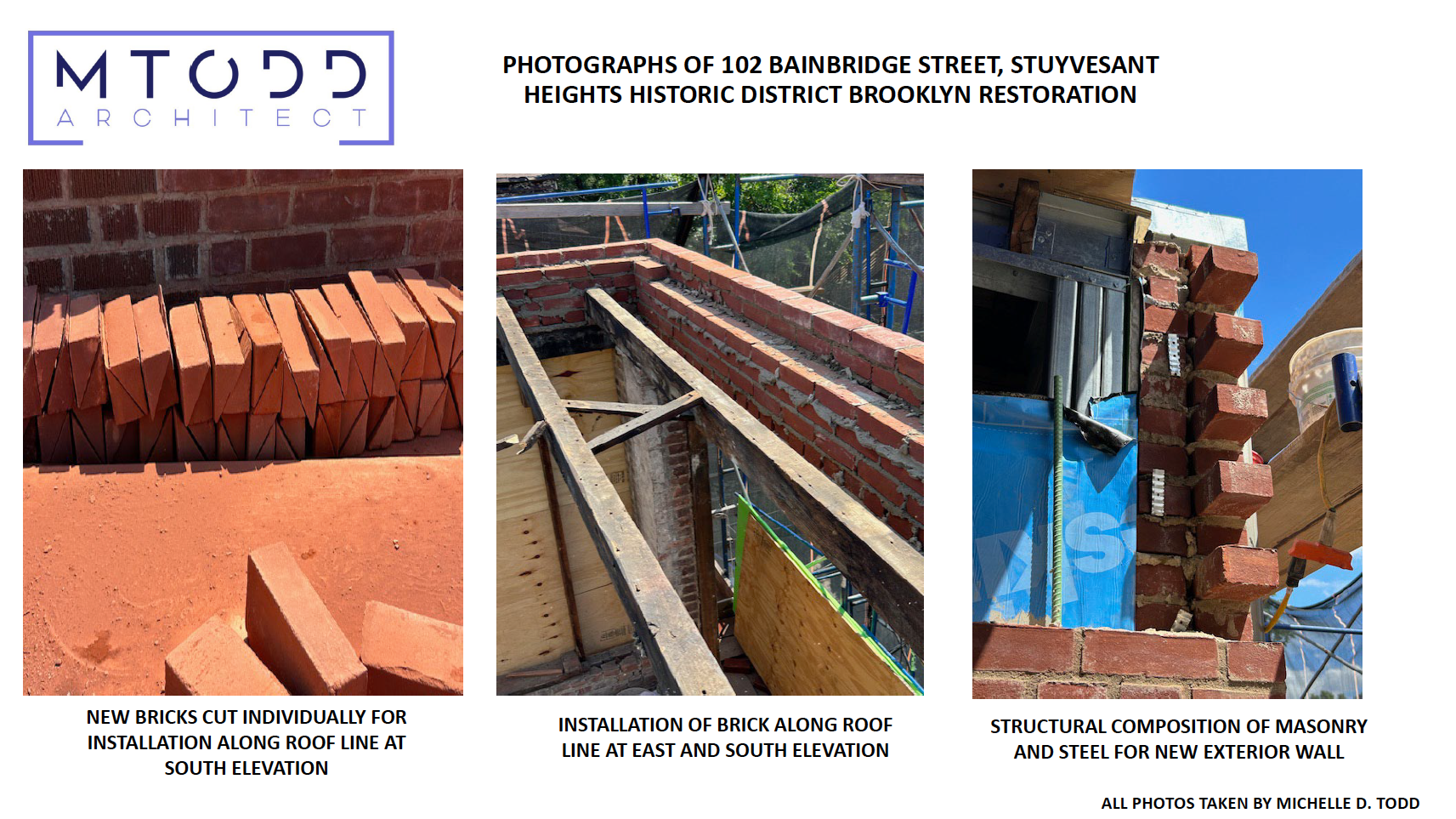
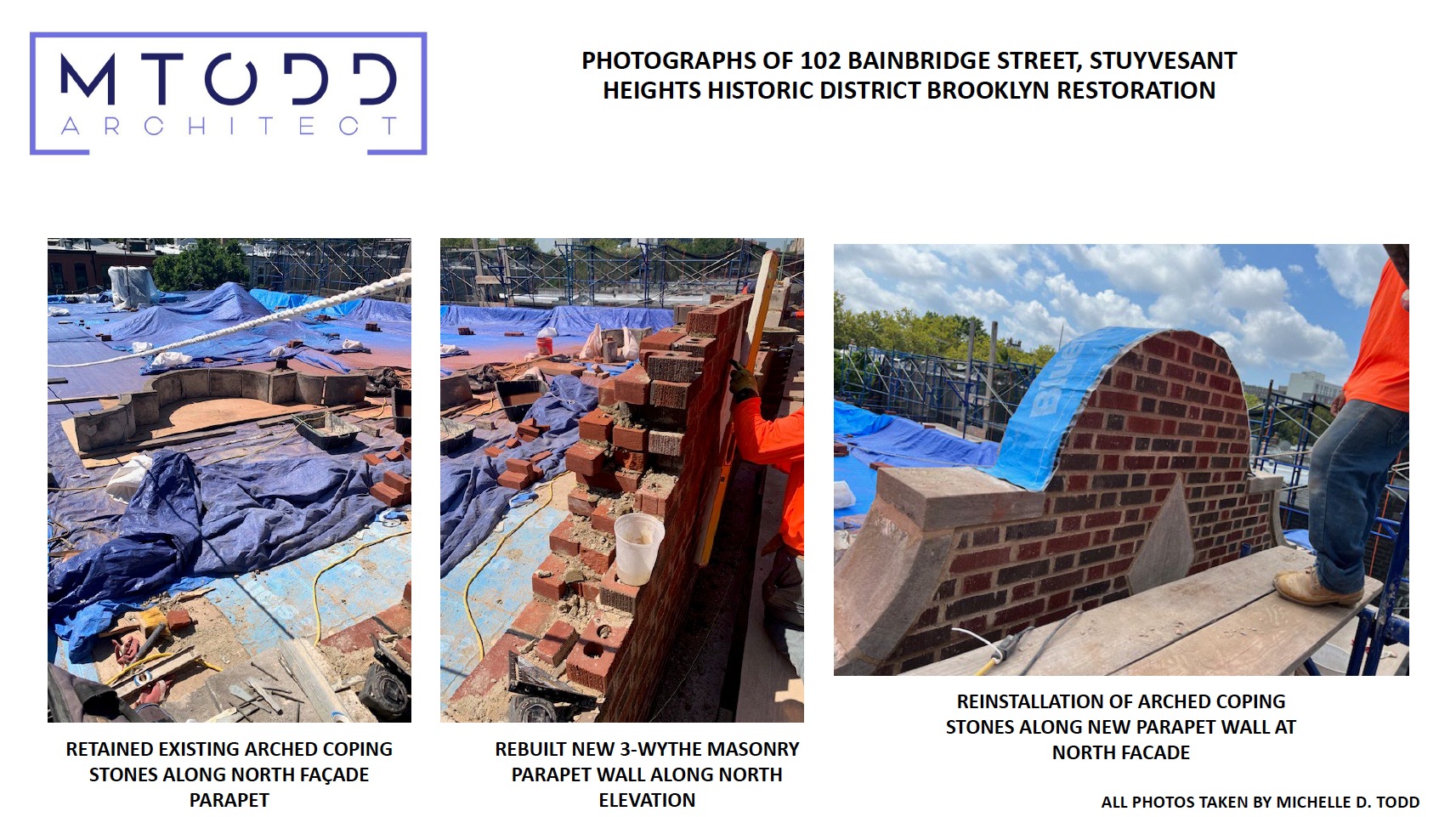
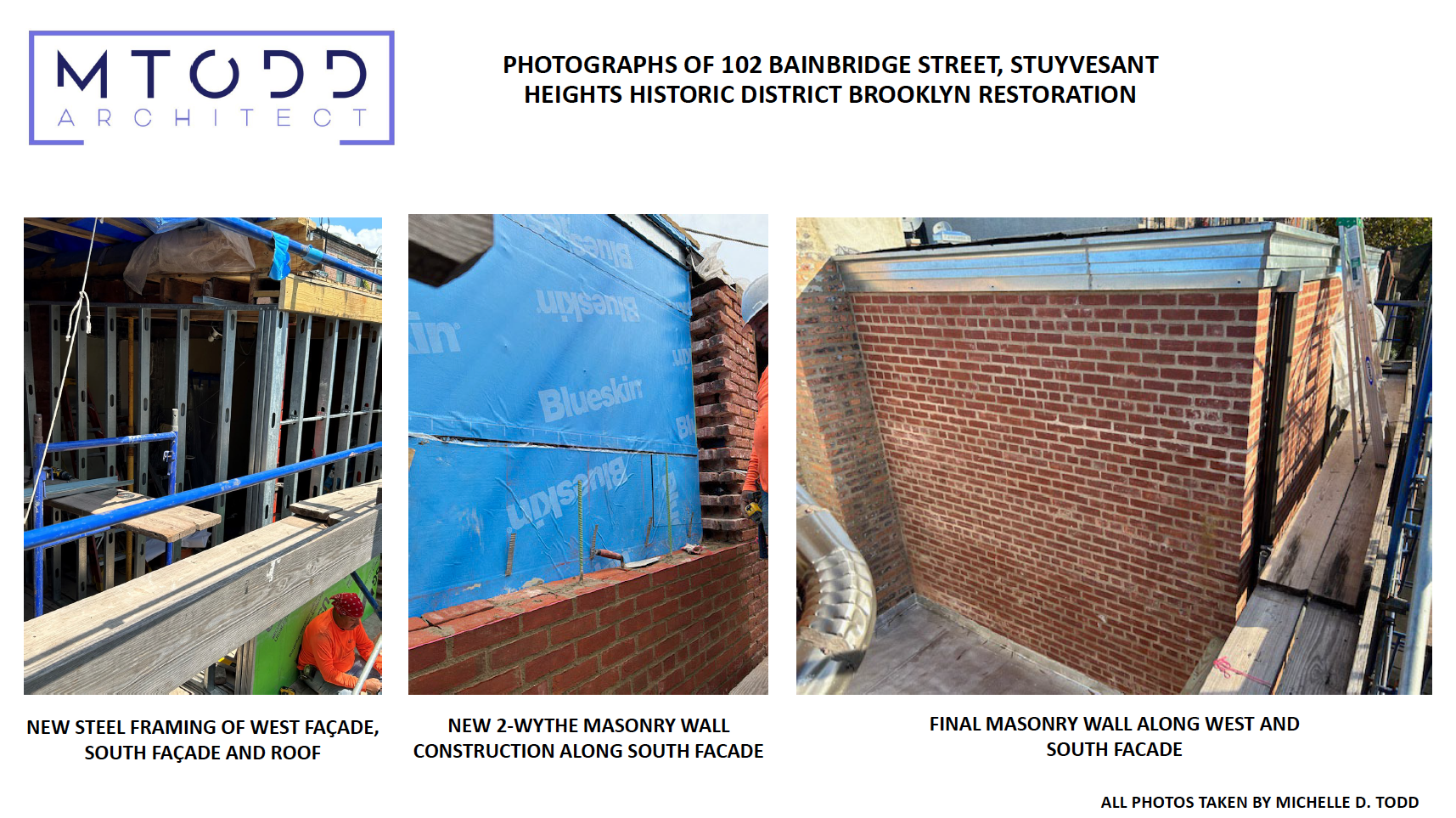
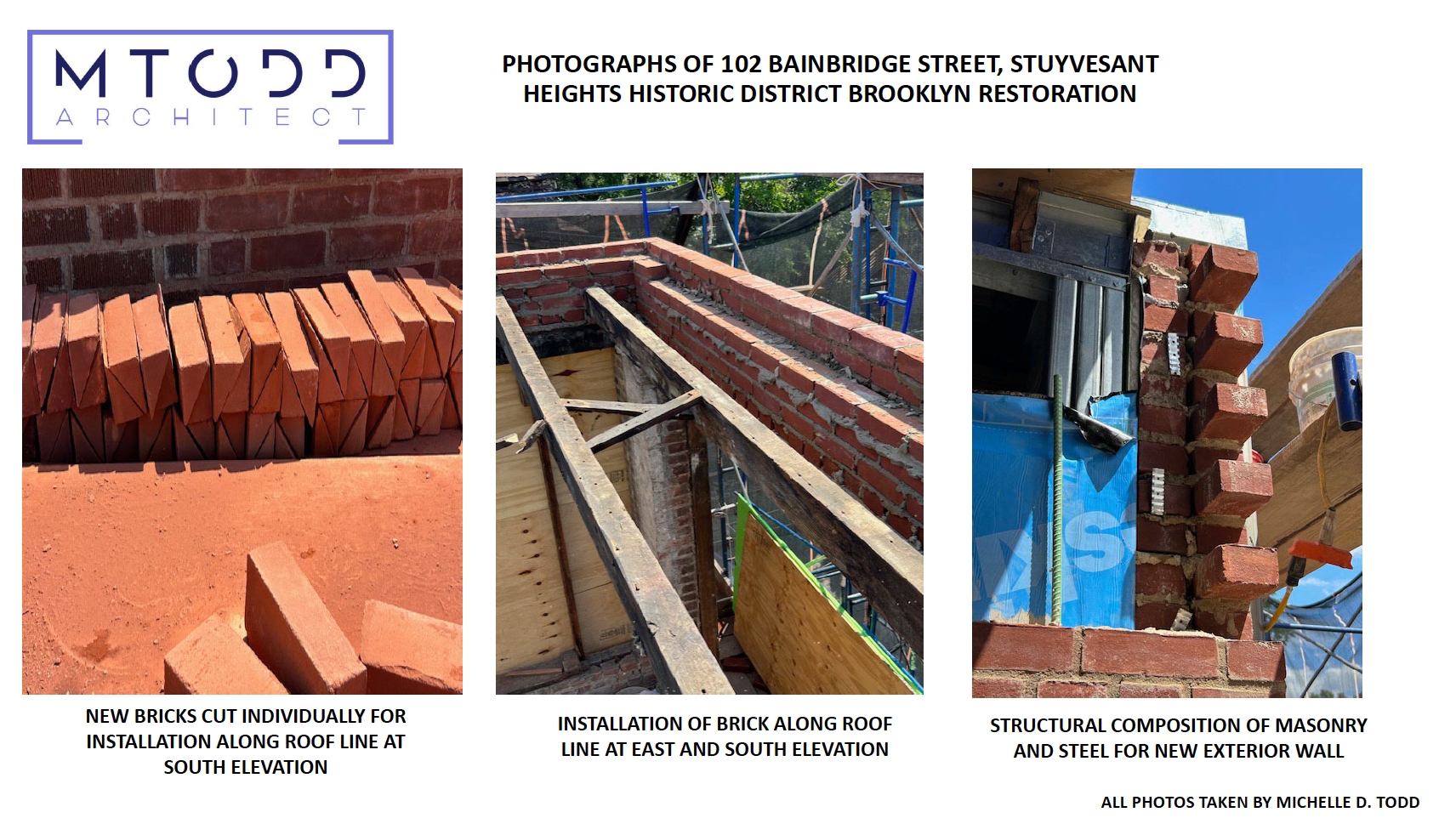
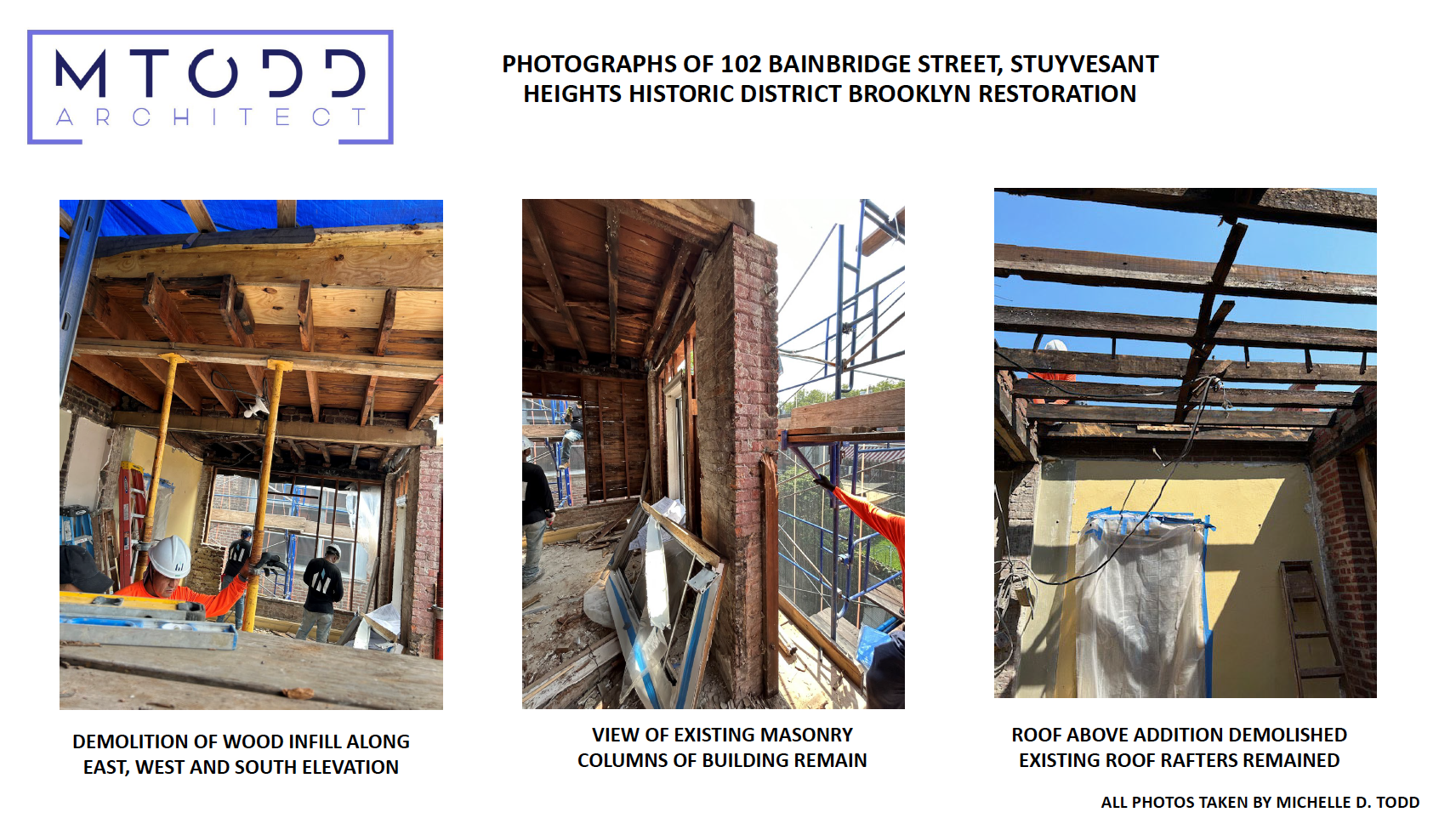
TRANSCRIPT
00;00;00;02 - 00;00;05;10
Doug Pat (DP)
Let's go inside the vault. The design vault.
00;00;05;12 - 00;00;34;05
Michelle Todd (MT)
So the whole idea was to fix the parapet and also to fix all of the step cracking within the facade. It was a beautiful building of brick in the front and the original status was that it had stucco on the very rear portion. We wind up finding out that this particular building, it wasn't brick behind it, it was actually wood.
So that therefore became more of an extensive project in which it wasn't just a renovation of the exterior facade, it was now a whole new addition and also an entire new rebuild.
00;00;34;07 - 00;01;01;23
DP
This is my guest, Michelle Todd. I'll share more about her shortly. In this episode from The Design Vault. We highlight Michelle's restoration project at 102 Bainbridge Street in Brooklyn's Bedford-Stuyvesant neighborhood. The Bainbridge Street renovation project is located in the Stuyvesant Heights Historic District. It was built within a row of buildings, which is a long group of houses planned to form seven freestanding architectural units.
00;01;01;28 - 00;03;46;13
DP
102 is situated at the end of the row. It's a modified Spanish residential style home with a triple arched loggia made of red brick laid in Flemish pond. The roof parapet rises at the center in an arch supported on concave shoulders. The restoration was begun to repair a buckling roof parapet, deteriorated walls, damaged pediment and cracking stucco facade.
Renovation work was extensive and a decision was made early not to replace the stucco, but rather leave and repair the natural brick masonry. The building scope also changed during construction from an exterior renovation to demolition and reconstruction due to construction material issues. Structural engineers were also consulted to create a necessary and unique wall construction method. The existing roof skylights, roof hatch and areas of limestone and bluestone were also repaired.
The project was also recently awarded the 2023 Lucy G. Moses New York Landmark Conservancy Award. Hi, I'm Doug Pat and this is Design Vault. Michelle Todd is an architect and principal of M.Todd Architects in Bedford-Stuyvesant, New York. Michelle has a master of science from Columbia University in architecture and urban design. She also studied at the École des Beaux-Arts in France.
Michelle grew up in Brooklyn's Bedford-Stuyvesant neighborhood in the 1970s. She knew she wanted to be an architect by the age of ten. Her interests today focus on urban planning and socially responsive architecture. After a brief stint at Perkins Eastman, she opened her own firm in 2008. Since then, she's worked for small and large corporations such as Snapple, the New York City Agency Office of Emergency Management, as well as private residential projects.
Her studio in Brooklyn, New York, focuses on historic renovations and additions, collaborating directly with clients and working closely with the general contractor during construction. Michelle's worked on Landmark designated buildings, bakeries, restaurants, schools and renovation projects. She's an adjunct professor at the New York City CUNY College and a licensed architect in New York State and Maryland. She's certified as a consultant with the International Institute of Building Enclosures, and Living Future accredited with the International Living Future Institute.
Welcome, Michelle. It's nice to have you with us today. So tell us a little bit about M.Todd Architects in Brooklyn. So where in Bed-Stuy are you located? What's the size of the firm? How long have you been around? And tell us a little more about project types.
00;03;46;16 - 00;04;19;19
MT
The firm is in the heart of Bedford-Stuyvesant on the whole Z Street. Been around since 2008 was almost 15 years as of March of this year, 2024. And basically the firm is small, is about three people, we specialize specifically in historical preservation, as well as residential private editions, commercial projects such as restaurants, bake houses and also schools. So basically you have a realm of achievement in different areas, which is commercial, residential and also business.
00;04;19;21 - 00;04;26;09
DP
So tell us a little bit about yourself. How long have you been practicing architecture and what's your role in the office as principal?
00;04;26;12 - 00;05;00;18
MT
I've been practicing architecture since 2008, when I received my license. However, I do have decades of experience before then in working at previous larger offices, in smaller offices to gain the experience I needed. Because, as you know, as an architect, you have to have at least three years working first in the field and then afterwards you're able to take the examination.
So once I did that, then just made initiative to just start my own practice. And basically I am the principal where I do a lot of marketing as well as clients in order to obtain business.
00;05;00;20 - 00;05;02;15
DP
And you said you have some employees?
00;05;02;21 - 00;05;13;16
MT
I do have employees. They're basically consultants. So basically I have a expediter. I have a drafts person. I have also my consultants, such as structural engineer, mechanical engineers.
00;05;13;19 - 00;05;21;08
DP
That's interesting. So you have an expediter that you guys use. And is that to make the process working with the city a little easier?
00;05;21;11 - 00;05;33;17
MT
It really does make it easier because as a person with a small firm, your hands are in everything. So to have somebody to be on the outside, to be able to do that type of work is appreciative and helpful.
00;05;33;19 - 00;05;46;05
DP
That's really cool. I mean, just as an aside, I hadn't really thought about the need for an expediter in a firm like that, but that makes perfect sense. So let's dig in here and talk about the home. How did your office get the project?
00;05;46;07 - 00;06;08;01
MT
I received the project in regards to as a dear friend, where I'm on the New York City Landmark Committee for Bedford-Stuyvesant specifically, and Community Board three, and he was a good member, Fred Jones, rest in peace. He had a friend who was in need of architectural services, so he recommended me to the client, which is the richest family, about this project.
00;06;08;03 - 00;06;10;01
DP
So you didn't know the clients before you got the job?
00;06;10;06 - 00;06;18;04
MT
I didn't know the clients. It was a friend of a friend, and he just talked highly about me and said that you should work with me in regards to this project.
00;06;18;06 - 00;06;24;26
DP
So give us a little history about the location. And was I correct in stating that the unit is an end unit?
00;06;24;29 - 00;07;08;00
MT
It is. It's in the beautiful, original, historic district of Bedford-Stuyvesant, which is known as Stuyvesant Heights, and it was established as a landmark district in 1971. So this set of buildings, it's literally between Stuyvesant and Lewis on Bainbridge. There's about 14 series of the buildings, and it's at the end row and there are Spanish style Renaissance buildings. That was created by W.f. McCarthy, who was an architect back in 1919.
And the unique thing about these buildings is that it's the only buildings I've ever been in with it has two staircases inside where there's one in the back and one in the front. So I guess back in those days they would have the servants come through the back and then the owners come through the front.
00;07;08;03 - 00;07;10;14
DP
Roughly, what's the square footage of the project?
00;07;10;16 - 00;07;13;09
MT
It's about 1200 square feet.
00;07;13;11 - 00;07;17;05
DP
And what was the scope and the programmatic requirements from the owner?
00;07;17;07 - 00;10;08;12
MT
Well, the original scope and program was that it was in terrible need in regards to the existing structure, the parapet was buckling. So on the north facade as well as the south and west facades, it was just crumbling. They were scared that it was going to fall down in some way. So the whole idea was to fix the parapet and also to fix all of the step cracking within the facade.
But then as we went along, we started to think also, it was a beautiful building of brick in the front. And the original status was that it had stucco on the very rear portion. Once we started to do the renovation was like, you know, we don't really need the stucco. It really looks beautiful with the brick itself. So we started to expose all the stucco, and by exposing all the stucco, we wound up finding out that this particular building, it wasn't brick behind it, it was actually wood.
So that therefore became more of an extensive project in which it wasn't just the renovation of the exterior facade, it was now a whole new addition and also an entire new rebuild. So we found out the history, and that was the nice thing about it. We really had to go back in the history of it. This is where the assistance of the expediter really came into play, because basically we found out that back in 1956, the building itself had a permit to actually do a addition because all of these beautiful houses.
What makes them so special in this neighborhood, too, is that they have their own private driveway, which many people don't have in that area. And also they have a garage. But then also on the second floor of each of these houses, they have a beautiful sunroom with a balcony. The person who owned the property at 102 Bainbridge, he basically wanted to make an addition.
So he eliminated that balcony and extended the whole square footage of the building so it can be enclosed. When we removed the stucco, we found out that instead of it masonry, he had it wood. So that was back in 1956. So we had to go back all the way to the building department to find out what the original drawings were, which we found out which were these beautiful blueprint drawings that you don't see anymore.
And it said that year they were legally supposed to have an addition, but it was supposed to be made out of brick, not wood. So that's where the whole expedition kind of came in. I had to go back to New York City building department, as well as the landmarks, because everyone was like shocked that it was wood versus masonry.
And we basically had to do a whole reconstruction. And that's where I guess the product of Glen-Gery came into play, because what happened to you is that on the back of the facade, all the bricks in the building weren't the same. The bricks in the front of the building were made out of Beldon, and it was a different type of color scheme.
But then when we removed the stucco in the back, it was a beautiful match with the Glen-Gery Kushwaha Calvert Plantation Middle Plantation, 52DD. It was a perfect match to it. Again, we had to go back to landmarks to make sure that they were approve of that brick to match what was in the rear facade that was being used.
00;10;08;15 - 00;10;17;12
DP
So what's interesting about the photographs that you sent is that the building looks as though some of these walls were completely taken down.
00;10;17;18 - 00;10;59;01
MT
It was because due to the fact it was stucco and I'm an architect that's very conscious about the environment. And stucco is something I concrete and it adds to the carbon footprint. So the whole idea was that this project specifically was to eliminate that process in really being more progressive and more enhancing to the environment. So that's why we didn't use stucco.
We wanted to just expose the beautiful masonry itself. And therefore, by eliminating the stucco, we saw the building was in need of much deeper repair than we expected. That was the thing, because in 1956 you figured that the contractors would be honest and they would do what they were supposed to do. But he wasn’t. And therefore that made this more of an adventure to get it right.
00;10;59;03 - 00;11;05;27
DP
So I would imagine there are a number of other buildings on that block that were also made of wood, that the interior wall construction. Is that correct?
00;11;06;00 - 00;11;44;10
MT
I don't know. That's the whole thing. What happened is, what makes this special is that this is the only house that has the addition. That's it. Everybody else has the sunroom. So this once in particular you thought that you would put it in masonry, but it's in it makes sense. First landmarks had to come and see it.
They were, like, shocked. Then I received the structural engineer, which was SOMA Engineering Firm, which is a great engineering firm. They came, they were shocked. The construction company that we work with, Naim Construction, all of us was basically shocked that this was behind the stucco because it looked like everything was fine. But when exposed, that's when we all gathered together as a team to like how we can resolve this.
00;11;44;16 - 00;11;52;22
DP
Interesting. Let's back up and talk a little bit about the plan of the building. I would assume it's just a large rectangle, two storey rectangle.
00;11;52;24 - 00;11;54;23
MT
Exactly. It was a two storey rectangle.
00;11;55;00 - 00;11;59;29
DP
And had you been contracted to design the interiors as well?
00;12;00;04 - 00;12;20;18
MT
I have for later date because what happens is based on the fact that now the photographs that you have here show of what it was existing. We went back to the premise of what it was back in 1919 when the solarium had these beautiful corner windows. So the design now is encompassing back the original style of that format.
00;12;20;20 - 00;12;25;05
DP
So you had to work with the city. How long did that process take?
00;12;25;08 - 00;12;53;21
MT
This is how it began. The project began in May 2020, during the pandemic. Then we actually had approval to start construction in April of 2021. Then all of these items, open issues about the facade not being what it was, and reconstruction, we basically spent about two years after that, and it was completed around October 20, 23. So it was back and forth with New York Landmarks as well as New York City Building Department.
00;12;53;27 - 00;12;55;09
DP
And the client had somewhere to live.
00;12;55;16 - 00;13;08;12
MT
He lived on the first floor. So the top floor. It was a blessing that he was able to live on the first floor while all this construction was going on. And in the top floor, basically, he had tenants, but then they moved out. When this major construction of us doing the rebuild.
00;13;08;15 - 00;13;09;07
DP
A lot of noise.
00;13;09;13 - 00;13;11;04
MT
It was a lot of noise.
00;13;11;04 - 00;13;11;23
DP
Very dusty.
00;13;11;24 - 00;13;15;00
MT
But it was fun.
00;13;15;02 - 00;13;24;10
DP
That's great. I'm interested as an architect about the drawings that you created in the very beginning. Did you work in 3D or just 2D?
00;13;24;12 - 00;13;33;28
MT
I worked in 2D, but then afterwards, when we started to look at what this condition that was taking place in the rear, I started looking at it in 3D and how it would be.
00;13;34;05 - 00;13;38;05
DP
And did you have to present drawings to a historic commission?
00;13;38;07 - 00;13;47;14
MT
Yes, we present it to Brian Blazak, is one of the senior preservationists on in New York City Landmarks. We had to show the drawings of what we planned to do.
00;13;47;16 - 00;13;48;26
DP
Exterior elevations?
00;13;49;03 - 00;13;50;24
MT
Yeah, exterior elevations.
00;13;50;26 - 00;13;58;25
DP
So again, backing up a little bit, you removed the stucco on one facade and replaced masonry on another. Is that correct?
00;13;58;28 - 00;14;25;03
MT
It's on the same facade. What happens is, is that the entire facade was placed in stucco. But then when we looked at the south elevation, so the windows were there, but it was infilled with wood. And that's what was shocking to everybody because basically it was really dilapidated and it also kind of made sense for the owner later on because he said his tenants always felt cold in that part of the room.
And it made sense because it was the wood and that masonry, there was no insulation whatsoever.
00;14;25;06 - 00;14;30;17
DP
So tell us a little bit about the new wall system that you guys had to create because of that condition.
00;14;30;19 - 00;15;17;03
MT
So the new wall system was still going back to what was historically done in regards to the rear facade was made out of three widths of brick, which basically is like three layers. And what we had to do is that we had to abide by what the actual, once we removed the stucco, what the actual pattern was, because it was a common bond, because as I stated in the beginning, the pattern in the front of the house was completely different than the pattern in the back of the house.
So once we established that, then we wanted to really make it structurally sound and we incorporated steel within the wall. So basically you have the three whiffs of brick on the outside, then you have the steel. It was stainless steel that made sure it was resource sustainably. And then we have our insulation and then our finishes in the inside.
00;15;17;06 - 00;15;26;25
DP
So the project sounds really interesting. Did you guys learn anything new about construction technologies or about building typologies in working on this project?
00;15;26;27 - 00;15;58;06
MT
Yes, the use of materials because again, was very selective about which materials we're going to use because since this building was already historically landmarked since 1919, we wanted to make sure that it lasts for another 100 years. So was very selective on who the steel came from, where the insulation came from, where the bricks came from. All of these were really mindful things and I think moving forward with other projects, I continue doing that, making sure that they are friendly to the planet as well as to the people who are going to live and utilize the buildings.
00;15;58;08 - 00;16;04;18
DP
So did the client bring the general contractor to the project or did you interview a number of contractors?
00;16;04;20 - 00;16;10;09
MT
We did interview a number of contractors, but then the client himself selected Naim Construction for it.
00;16;10;12 - 00;16;15;19
DP
And clearly there's a lot of masonry work. Did you have any challenges finding a good mason?
00;16;15;21 - 00;16;45;27
MT
Oh no. He has very excellent masons and they were very accommodating because we had to go back and forth with New York City Landmarks when we were selecting the bricks where we had to actually do a sample of the wall where the wood infill was of how the brick was going to look. So one of his masons, George, was really who's one of the oldest ones there.
It has most experience. He was very patient. We went on the scaffolding and it was a really cold day, but we did the whole mock up and it came out beautiful. And therefore Landmark said, Yes, go with it.
00;16;45;29 - 00;16;49;16
DP
So you did the mock up and the city came out and took a look at it?
00;16;49;19 - 00;16;56;05
MT
No, we took photographs and then afterwards they were like, because it was cold.
00;16;56;07 - 00;17;05;24
DP
So the city doesn't like to go out on cold days? I think we’ll leave that in there. That's good. So I assume the client's living there now?
00;17;06;02 - 00;17;09;17
MT
He is. He's living in the bottom floor still, but he's happy with the work.
00;17;09;20 - 00;17;12;25
DP
So is it complete? And he has a tenant on the second floor?
00;17;13;00 - 00;17;22;21
MT
He doesn't have a tenant on the second floor. And it's not quite complete yet because now we're just waiting for the historical windows to come in. So that is the last crème de la crème.
00;17;22;23 - 00;17;24;27
DP
And who is the manufacturer of the windows?
00;17;25;03 - 00;17;36;10
MT
It is Norwood Manufacturers, a Canadian company. And again, it was very selective on them because the way they use and harvest wood in order to make the windows, we're really mindful about that.
00;17;36;17 - 00;17;39;23
DP
Interesting. Are they double glazed? Triple glazed?
00;17;39;25 - 00;17;49;03
MT
They're triple glazed, low e glass index and they're quite beautiful. They're the original to what was there before of the windows? So they're replicating those.
00;17;49;05 - 00;17;57;00
DP
So I'm curious in terms of color, you were able to find a brick that you were happy with. You said that matched on the exterior.
00;17;57;02 - 00;18;12;16
MT
The contractor has suggested he was like, this will be a perfect break. I did research and was a Glen-Gery Kushwaha Calvert 52 DD Middle Plantation. That was the one that was selected. And when we put it in place, it was perfect to what was there from 1919.
00;18;12;22 - 00;18;15;27
DP
So do all these row homes, they all must look the same?
00;18;16;02 - 00;18;45;16
MT
They basically all look the same. And the other fascinating thing too, with the project, when we were doing the demo for the wood infield, all the bricks, I learned this like recently from my practice that the bricks that we were removing, that were there all had the names of the brick companies on there. And you don't see that anymore in which they were actually etched into the brick.
I was like, Wow, It's like, fascinating. So it was like an archeological project in the same way of doing something better for the building for another hundred years.
00;18;45;19 - 00;18;52;24
DP
So when you guys put these new windows in, what about the color? Can you do whatever color you want or the colors have to match the other homes.
00;18;52;26 - 00;18;57;13
MT
The colors have to match. It is going to be made out of wood, but they're going to be of a white finish.
00;18;57;16 - 00;19;00;10
DP
And they have to be traditional in style to match the others.
00;19;00;16 - 00;19;01;06
MT
Exactly.
00;19;01;06 - 00;19;11;17
DP
Interesting. So, Michelle, you've been an architect for some time. Based on what you know today about being an architect, you have any words of advice for your younger self or maybe architects coming up in the ranks?
00;19;11;19 - 00;19;41;21
MT
I would say don't quit on yourself. That's for me personally, as a woman and a woman of color in this industry, to always just believe in yourself, that what you find really interesting and powerful within yourself will just keep working at it and you'll get recognition. But it's not really about the recognition. I've always known I wanted to be an architect.
I feel architecture is like a stewardship. You are helping other people to obtain their desires and dreams and designs, but then also, too, helping the planet.
00;19;41;24 - 00;19;49;23
DP
So, Michelle, it's been great to have you here today. Thank you so much for your time. Where could people go to learn more M.Todd Architect and yourself?
00;19;49;26 - 00;19;56;06
MT
You can find me on my website at MToddArchitects.com and then also I'm on LinkedIn.
00;19;56;08 - 00;19;58;10
DP
Well, thank you very much. It has been great to have you.
00;19;58;17 - 00;20;00;24
MT
Thank you so much. Appreciate the opportunity.
You May Also Be Interested In
We Can Help With Your Next Project
Discover the latest + greatest in design trends, industry news & pro tips from pros.
For all of your project needs, you’ll find everything you need at a Supply Center.
Let Us Know How We Can Help!